FLEXIBLE WATERPROOF FOILS

Flexcoat is developed for covering full surface of substract. The most significant feature is strong elasticity with soft touch.
Flexcoat is waterproof and airproof. It is not self-adhesive. Polyurethane based adhesive compatibility. is for both textile and leather surfaces. Total thickness is 19 microns and 4 microns part is transferrable.
Flexcoat is used for leggings with elastic fabrics in textile industry. It is also used in leather industry to have double side skin and increase the quality of skin.
In addition to the transparent foils, more than 20 different color options are available.
TEMPERATURE: 145-150°C
PRESSURE: 6 bar
SPEED: 3-5 m/min
LENGTH: 3 inch 200/500/1000 m
Customer-specific length can be produced upon request
WIDTH: 150 cm
19 micron
(4 microns transferrable)
Applicable for both rotogravure or spray coated adhesive surfaces
Reverse wash is recommended at 30°C for 50 minutes at gentle washing programme of washing machine
Not suitable for dry cleaning
Iron at "one dot" as reverse ironing
Recommended shelf life is 6 months at dry and cool area
Web sitesi, Kullanıcının bu site tarafından maksimum gezinmesini kişiselleştirmek ve kolaylaştırmak için çerezleri kullanabilir. Kullanıcı, tarayıcısını tarafımızdan gönderilen çerezlerin kurulumunu bildirecek ve reddedecek şekilde yapılandırabilir.
Advantages of Flexcoat Foils
Flexcoat coating foils also have a covering effect on light surfaces.

Being compatible with stretchable fabrics, it does not make knee and can return to its previous state.
It is succesful in creating artificial skin on suede for double sided coats.

It can be used in outdoor fabrics with its structure that is completely water and air proof.
Flexcoat Foil Printing Stages
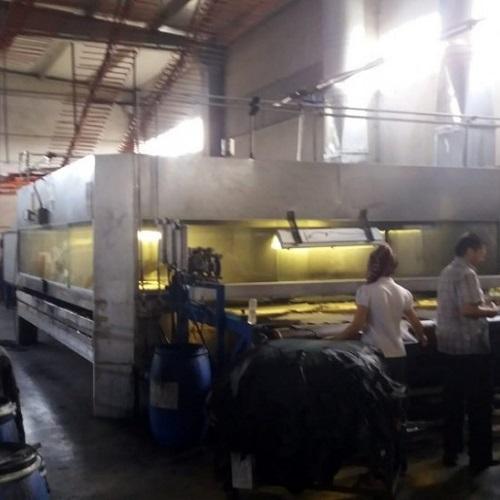
1-A
Glue Application with Spray
Especially in applications on genuine leather, water based elastic adhesives are applied to the surface manually or with automatic machiines and left for drying.

1-B
Glue Coating with Engraving
In roll to roll printing applications , a precise amount of solvent based adhesive is applied to the surface where Flexcoat foil to be transferred with engraving machine.
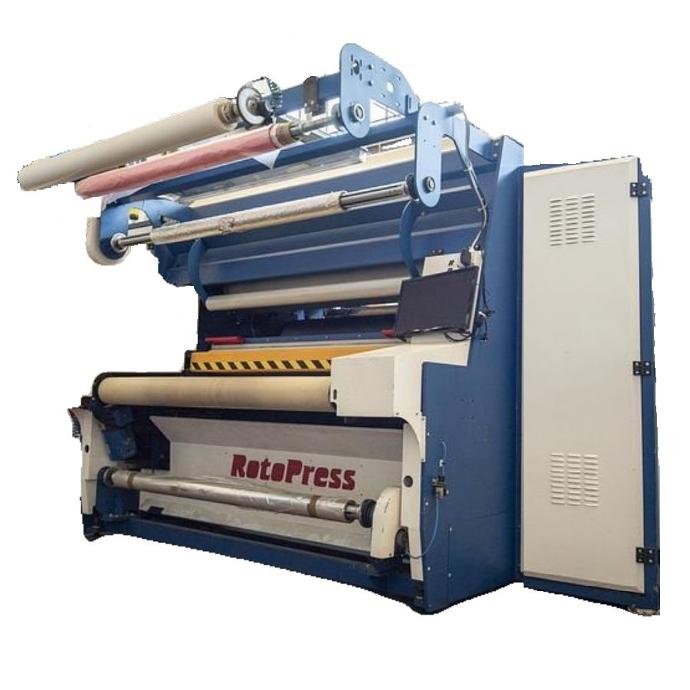
2
Transfer with Rotopress
Front feed rotopresses, they are the most suitable option to prevent bubble formation in the airtight product even if the transfer is made on to the partial section.
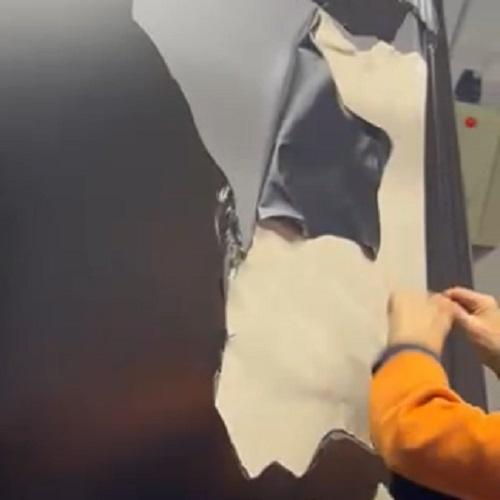
3
Peeling of the Carrier Film
Due to the characteristics of polyurethane, the applied Flexcoat should be separated carefully to prevent its fringes from sticking to itself.
Examples of Glue Application and Flexcoat Printing Machines
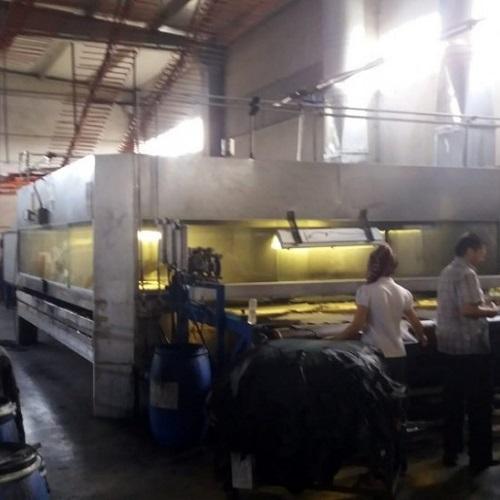
Spray and Air Gun Coating
Especially applications on genuine leather, water based elastic adhesive applied to the surface that would create a durable surface for Flexcoat.
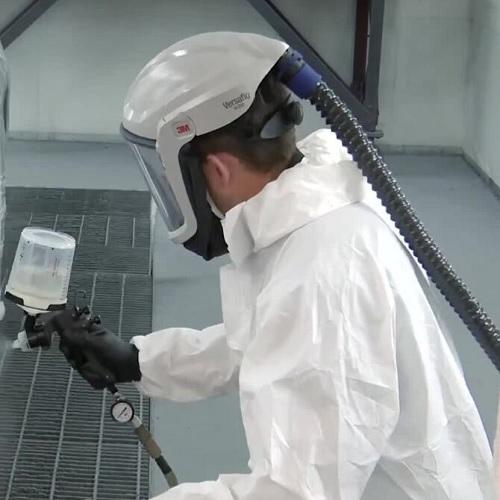
Glue Application by Hand
Glue applied by hand provides opportunity to display the durable and elegent characters of Flexcoat products which have waterproof and elastic structure.
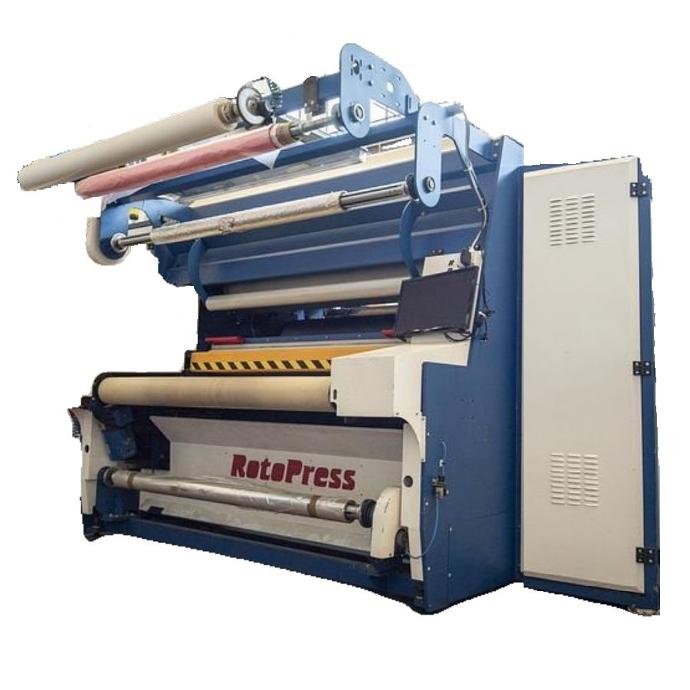
Rotopress
Flexcoat can be transferred using rotopress machine which was previously applied by hand or spray application.

Gravure Cylinder Coating
Especially in textile coatings, Flexcoat is also transferred while glue is applied with gravure cylinders.
Other Products can be used for Flexcoat Foil Printing
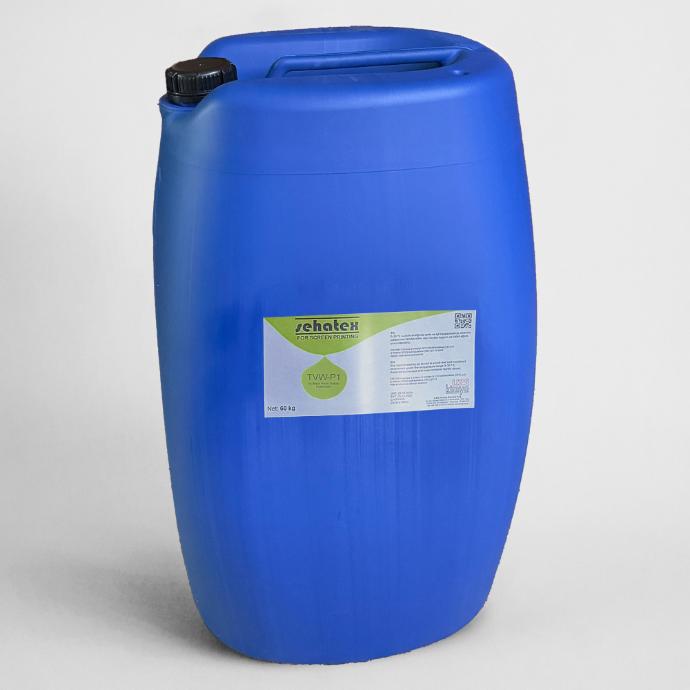
Water Based Adhesive
It can be used for both roll to roll and partial printing and suitable for spray application.
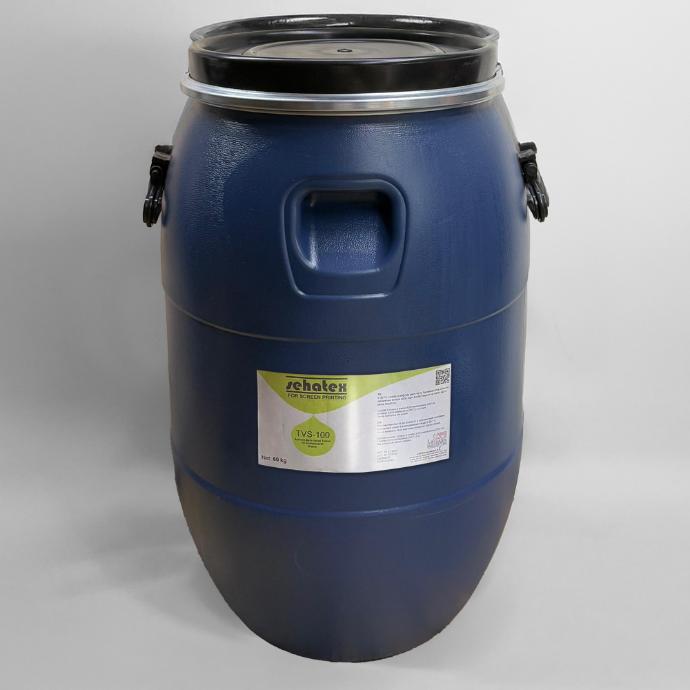
Solvent Based Adhesive
Adhesives that are used in smog gravüre printing machines.
General Warnings about Foil Printing Application
This information provided on this page about foil printing is for general guidance purposes.
The information provided under the headings of Flexcoat advantages, Flexcoat printing stages, glue application and Flexcoat printing machines may not cover all the aspects. Application may require professional machines and expertise.
Even when performed with the same machines, applications depend on specific adjustments and some critical variables. These include foil, adhesive and the surface on which the application is made. For example; the type of solvent used in diluting the solvent-based glue, the transfer grammage of the gravure mold can directly affect the performance of the product. A fast-drying glue recipe can cause the foil to wrap around the gravure cylinder. Leathers separated after printing are very open to contamination and can be stained very quickly after 1-2 days due to factors such as dirty hands.
Flexcoat, which does not have the ability to adhere to fabric or leather, can only be transferred with the help of an adhesive that can adhere to the surface it will be transferred to. The quality and properties of the glue; the fact that it is applied under the right conditions, directly affects the result. The final product should be tested first, the necessary tests should be done at least 1 day later, and then production should be started.
Foil printing involves some technical complexity than traditional printing methods. It is often performed by subcontractors rather than integrated facilities such as dyehouses or tanneries. By addressing weak points in this process, predictable results can be achieved with ease.
Troubleshooting and Technical Information page is for theoretical insights into common issues.
For technical support, feel free to contact our company.